Intoduction
At the request of Mr. Rennie Coombs acting
for Beadcrete Pty Ltd, the Building Research Centre undertook
tests of a polymer-modified topping mortar impregnated with
glass beads produced by Beadcrete with a view to investigating
aspects of its serviceability when used as a lining material
for concrete swimming pools. When finished, the glass beads
form an exposed aggregate giving the surface a distinctive
reflective appearance. Beadcrete reflective mortar is usually
applied in thicknesses in the vicinity of 8-10mm.
|
|
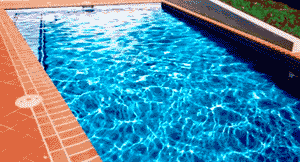 |
In this program of work, the material was examined
for its shrinkage and adhesion characteristics. The dry mortar
constituents were supplied and mixed by Beadcrete before being
applied by Beadcrete staff to concrete substrates supplied by
the BRC. The formulation tested used a dry acrylic agent as the
main modifier.
The program of testing was suggested by the BRC
after discussions with Mr. Coombs. Specimen material was delivered
to the BRC's Randwick laboratory where the tests were carried
out from September to December of 1998. Other than the mixing
and application of the mortar to substrates, the work was undertaken
by BRC staff under the supervision of the author.
Method
Shrinkage: As required by the procedure
of ASTM C596, four mortar prisms each measuring 285 x 25 x 25mm
were cast using the Beadcrete supplied by the company and mixed
by the BRC to the company's specifications. Targets were incorporated
in the ends of the prisms allowing their change of length to be
measured using a comparator. The prisms were moist cured in (he
moulds for one day and water cured for 2 days before being placed
in a controlled environment for drying at 23 ± 1 °C and 50 ± 5
% RH. As specified in the Standard, the changes in length of the
specimens were monitored at regular intervals over a 28 day period
to arrive at a
Adhesion to Substrate: Beadcrete staff
applied the reflective mortar to a depth of 20mm over concrete
substrates, 250 x 250 x 40mm thick prepared by the BRC. Two of
the substrates were several years old - their top surfaces were
prepared for the application of the mortar by light wire brushing.
The other four substrates had been prepared three weeks before
- their top surfaces were finished with a wooden float to aid
adhesion of the mortar. The surface preparations are representative
of Beadcrete's current practice.
After having been mixed to a cake mix-like consistency
and trowelled into place, the material was allowed to set for
30 minutes before the top layer of the mortar was washed off using
a sprinkle head nozzle to expose the glass beads. The mortar was
applied on the 7th of October 1998 after which the specimens were
dry cured at 23°C and 50% RH. until the 20th when they were placed
in an accelerated weathering apparatus. The accelerated weathering
regime consisted of six cycles per day of immersion in 10% salt
solution followed by drying under heat lamps to 60°C. A control
specimen of new and old substrate was left un-exposed to weathering.
After exposure to each of 30, 60 and W) cycles
of weathering, the adhesion strength of the bond between Beadcrete
and the substrates was assessed by a pull-away test. A 60mm diameter
core cutter is passed through the topping into the substrate creating
a circular island of topping 60.5mm in diameter. A steel plate
is epoxy bonded to the (op face and the disc of mortar pulled
away from the substrate. The force required to separate the mortar
disc from the substrate is assessed by an electronic load cell
and the calculated ultimate tensile stress over the circular area
is a measure of the bond strength attained.
Results
Shrinkage: Figure 3.1 is a curve of shrinkage
strain (average of four prisms) plotted against time. The dry
shrinkage is corrected to allow for the small expansion that occurred
during the water curing period. The average 28-day shrinkage of
1011 microstrain observed is not considered excessive for a mortar.
Figure 3.1
Adhesion strength: The results of testing
of the strength of the bond be-tween Beadcrete and (he concrete
substrates arc summarised in Table 3.1. The results suggest slight
decrease in bond strength with exposure to repeated cycles of
and immersion in salt water and drying with heat. The bond strengths
recorded are all significantly over one Megapascal, an often-quoted
level for acceptable adhesion of renders and mortars. Some exposed
specimens failed prematurely due to shortcomings in the epoxy
bond to the salt affected top surface.
Table 3.1
Conclusions
When mixed and applied according to the suppliers
instructions, the glass bead impregnated polymer modified mortar
"Beadcrete", made to the formula tested by the Building Research
Centre in late 1998, shows an acceptable level of shrinkage for
use in the rendering of swimming pools.
When applied over wood float finished concrete,
"Beadcrete" shows a high adhesion strength to the substrate which
is not greatly affected by repeated changes of temperature and
moisture. A similar strong adhesive bond was observed when the
substrate was older concrete whose surface was prepared by wire
brushing.
The results suggest that the adhesion of "Beadcrete"
to the wood floated concrete substrate is not affected by later
contact with salt water.
For Beadcrete Performance Warranty , contact your local distributer.
Return to: Pool Plaster
Information and pictures:
|